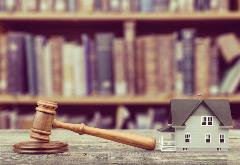
By S. Michael Lynn
As established in Part One of this article, published in the May/June 2013 issue of Update magazine, there are no standards or requirements for well and septic inspections in Virginia. What should agents expect?
Defining the benchmark for a pass or fail grade is often the most difficult part of the well or septic inspection. The regulatory standards for conventional systems and alternative systems differ. For either system, however, the presence of raw or partially treated sewage on the ground, backing up into the house or contaminating groundwater is a condition for which the health department can take enforcement action. Alternative systems are held to a somewhat higher standard in that the owner is required to have the system operated and maintained by a licensed operator.
Tank Evaluation
Some systems have as many as four tanks, and pumping each of those out could cost as much as $1,000. Most inspectors want to ensure that the required inlet and outlet tees, filters and water stops are in place. This requires pumping to a certain degree. Most inspectors also want to look for signs of structural integrity. This requires septic tanks and treatment units to be pumped out in most cases, but pump chambers can usually be evaluated without pumping.
Common Problems and Solutions
To allow some room for interpretation by inspectors and negotiation between buyers and sellers, the NVAR Well & Septic Addendum does not define what constitutes a septic malfunction. During septic inspections, one approach uses three basic benchmarks: Safe, Adequate and Proper. These definitions are derived from a draft policy created by The Virginia Department of Health.
Safe: The onsite sewage system is functioning in a forward flow manner and is not currently nor is it expected to adversely affect public health or groundwater supplies, as long as routine maintenance and repairs are carried out.
Adequate: The onsite sewage system is sufficiently designed and constructed to account for the sewage flow and strength from the facility.
Proper: The local health department has issued an operation permit or other approval for the system, or there is sufficient evidence to suggest that the system was legally installed.
These benchmarks can be explained using an automobile analogy.
Safe: Based on the inspection results, the inspector is fairly certain that if the car is driven down the road, its going to go when the accelerator is pressed, its going to stop when the brakes are pressed, and at a normal speed the engine isnt going to explode and the wheels arent going to fall off. It may need a little bodywork and new tires in a few months or a year, but its not going to leave the driver stranded as long as it is maintained.
For an inspector to label a septic system safe, the owner should expect to flush the toilet, take a shower and possibly face some maintenance requirements, but in the near future sewage is not likely to come to the surface, contaminate the environment or back up in the house.
Adequate: Consumers cant expect a VW bug to be a reliable commuter car for 10 people in a car pool. Even transporting 10 people in it on an occasional basis is not realistic.
Similarly, a six-bedroom house with two kitchens and an in-law suite using a three-bedroom septic system warrants a closer look. If the homeowners are just a family of four and arent going to use the six bedrooms full time, then an inspector might find that the system is adquate. Sometimes agreeing on what constitutes adequate is the biggest hurdle for inspectors.
Proper: Does a car have a clean title? If taken to DMV, will the owner be able to register it? Was the car produced to U.S. standards, or was it built in someones garage?
A similar analysis applies when considering whether a septic system warrants a proper rating. For an inspector to deem a system proper, he or she should be reasonably sure that the system was permitted by the health department, installed by a licensed contractor, inspected and approved.
County health departments handle inspections differently, some strictly by the book, and others just want the buyers and sellers to be informed about what is being bought or sold. Often, inspectors follow the stricter definitions of Safe, Adequate and Proper when there is an application for a building permit for a deck, pool, addition or garage.
The Five Most Common Septic Inspections Problems:
1. The number of bedrooms in the house does not match: (a) the number of bedrooms that the septic system is designed to handle; (b) the number of bedrooms that the house is advertised to have; or (c) the number of bedrooms that the tax assessment says the house has.
Virginia regulations require that systems be designed for two full-time occupants per bedroom. If there are more bedrooms in the house than the system is designed to accommodate, there are several methods to address the issue. The buyer and seller can agree on the capacity discrepancy and understand the limitations of the system. There may be a method to upgrade the onsite system to match the number of bedrooms. Owners may apply for a conditional operations permit from the local health department acknowledging the discrepancy.
Cost to Resolve: $0 if the parties agree on the discrepancy, up to $10,000 to expand the system to accommodate more bedrooms
2. Risers, lids and covers cracked or leaking: Can be unsafe or can allow groundwater to leak into system causing system being overloaded with water and experience premature failure.
Cost to Repair: $100 - $1,000 to seal leaks in tanks
3. Distribution boxes in disrepair: Cracked lids, boxes not level, deteriorated boxes. These conditions cause uneven distribution of effluent and can cause portions of the drain field to be overloaded.
Cost to repair: $750 to $1,200 per box
4. Root intrusion into distribution boxes and headers. This condition cracks concrete components and blocks lines, causing uneven distribution and/or total blockage of flow.
Cost to Repair: $500 to $3,500 if boxes and headers need to be replaced
5. Header Lines crushed or blocked with sludge. Usually the result of not pumping the tank often enough or heavy use, which causes sludge to be passed out of the septic tank and into the distribution box and headers.
Cost to Repair: $1,200 to jet sludge out, to $3,500 to replace boxes and header lines
Worst-Case Scenario:
the system is failing with sewage on the ground
The system is not functioning in a forward flow manner
The inspector doesnt think the system will return to a normal function if an unoccupied property is re-occupied.
In the past, the only option was to add a few lines or install a new system. With the advancement of alternative systems, there are options available that solve the short- and long-term problems without a total system replacemen:
Adding treatment to help a system recover
Installing new trenches in between failed trenches
Installing a drip system over the top of failed trenches
However, some situations will require that the old system be abandoned and a new in-ground or discharge system installed. Cost to Correct? $4,500 to $45,000
The perspective discussed in this article is only one of many. Firms, inspectors and health department officials may have different opinions. Agents should encourage clients to discuss their options with their inspector of choice or the local health department.
S. Michael Lynn is president of SES Mid Atlantic, LLC. He can be reached at This email address is being protected from spambots. You need JavaScript enabled to view it..">mlynn@ses-company.com.
Editors Note: This is part two of a two-part series on Well & Septic. Part one can be found in the May/June issue of Update magazine.